CLEANING & PRETREATMENTS
Cleaning and conversion coating pretreatments provide the essential foundation for enhanced adhesion, corrosion resistance, and long-lasting performance.
Pretreatments for Coatings in North America
Metal Finishing Companies in CT
At Giering Metal Finishing, our cleaning and conversion coatings services provide the critical foundation for superior metal finishing. These processes enhance the durability, corrosion resistance, and overall performance of metal components, ensuring they meet the highest standards in quality and longevity. From automotive to aerospace, we work with a wide range of industries to deliver precision results tailored to your needs.
What Are Cleaning and Pretreatments?
Cleaning and pretreatment for coatings involve the preparation and treatment of metal surfaces to improve adhesion, prevent corrosion, and optimize the finishing process. By cleaning and pretreating the surface, we ensure that coatings such as paint, powder, or e-coat adhere properly and perform effectively. Conversion coatings, such as phosphating, provide an additional layer of protection by chemically altering the surface to enhance its resistance to rust and wear.
Substrates We Work With
We specialize in working with a diverse range of substrates to ensure optimal coating performance. Each material requires a unique approach to achieve the best results, and our expertise ensures flawless finishes tailored to your product’s needs.
Partner with Us for High Quality Metal Finishing
When it comes to cleaning and conversion coatings, Giering Metal Finishing is your trusted partner for quality and reliability. Contact us today to discuss your project requirements and learn how our expertise can enhance your products.
Let’s get started—call us at (203) 248-5583 or contact us today.
RELATED SERVICES
Quality & CONSISTENCY
Unmatched Quality, Proven Standards
At Giering Metal Finishing, quality is the cornerstone of everything we do. Utilizing advanced tools and rigorous quality control processes, we ensure each finish meets the highest standards for durability, consistency, and performance. From precise film thickness measurements to meticulous inspections, our team works diligently to adhere to your exact specifications.
Whether it's achieving flawless finishes, color matching, or delivering unmatched corrosion protection, our commitment to excellence ensures consistent results across every batch.
Our pretreatment processes
meet the following military
specifications:
industries
Common Uses for Cleaning & Conversion Coatings
At Giering Metal Finishing, cleaning and conversion coatings play a vital role in preparing metal surfaces for enhanced performance. These coatings provide superior corrosion resistance, ensuring your parts withstand harsh environments. They also improve adhesion for finishes such as paint, powder coating, or electrocoating, making them essential in industries like aerospace, automotive, and defense.
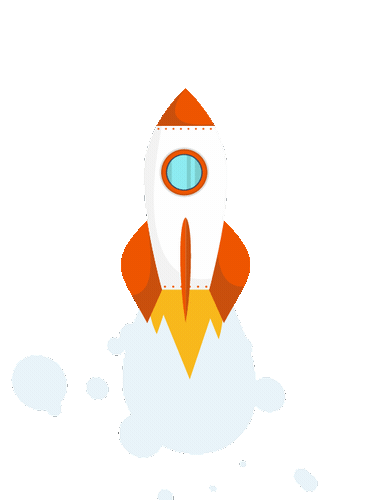
Need it fast?
Expedited Services Tailored to Your Deadlines
At Giering Metal Finishing, we understand that sometimes strict deadlines call for urgent solutions. Our expedited services ensure your order is prioritized and completed faster than standard lead times, helping you stay on track without compromising quality.
Frequently Asked Questions
What is the purpose of cleaning and conversion coatings?
Cleaning and conversion coatings prepare metal surfaces by removing contaminants and enhancing adhesion for subsequent finishes, while also providing corrosion resistance to improve durability.
What types of conversion coatings do you offer?
We offer a variety of conversion coatings, including iron and zinc phosphating, to suit different applications and performance requirements.
Which industries benefit from cleaning and conversion coatings?
Industries such as automotive, aerospace, military, medical, and industrial manufacturing benefit from cleaning and conversion coatings to ensure product reliability, longevity, and superior finish quality.
WHY CHOOSE US
Choosing Giering Metal Finishing means partnering with a team committed to precision, quality, and reliability. With decades of expertise, cutting-edge technology, and trusted relationships with fellow finishers, we deliver tailored solutions and reliable recommendations beyond our specialty.
70 Years of Experience
Decades of proven expertise in solving complex challenges.
Comprehensive Capabilities
We offer a full range of finishing services under one roof.
Customized Solutions
Every project is tailored to meet specific industry and requirements.
Exceptional Support
Our team works closely with you, providing transparency.